The Use and Maintenance of Car Lift – Basic Knowledge Lecture
Mastering the Basics: Essential Knowledge on Car Lift
Published in “Automotive Repair and Maintenance”
Car lift have been a key component in the automotive maintenance industry since the 1980s, replacing traditional pit work and greatly contributing to the efficiency of the field. As the automotive market rapidly expands, car lift are drawing more attention due to their essential role in vehicle maintenance. Their proper operation and maintenance are crucial for ensuring the safety of both equipment owners and automotive repair technicians. This article will focus on the operation and maintenance of commonly used car lift, providing guidelines for safer and more standardized practices.
Two Post Car Lift
Two post car lift can be categorized by their transmission system—either mechanical or hydraulic. Structurally, they are divided into two types: the bottom plate two post lift (Figure 1, also known as the floor plate lift) and the gantry two post lift (Figure 2).
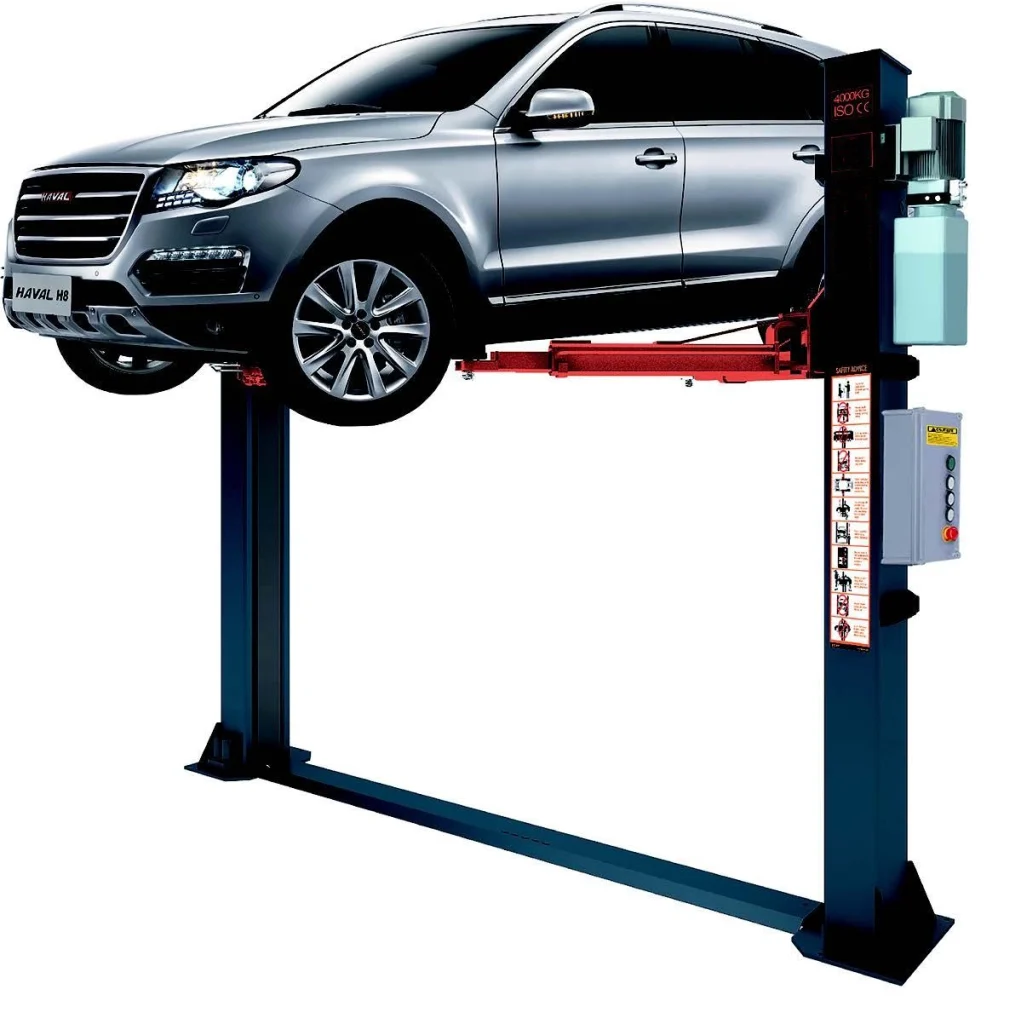
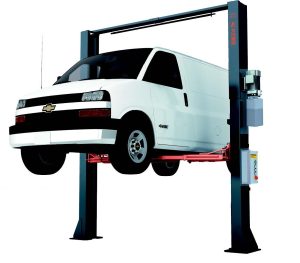
Hydraulic two post car lift are currently the dominant products in the market. These lifts are further classified based on their drive mechanism (single-cylinder or dual-cylinder) and the method of lowering operation. Lowering can be controlled either manually via a hydraulic pump station with a manual release valve, or electrically using a descent button to operate an electromagnetic release valve.
Safety unlocking mechanisms also vary:
- Electric unlocking: Controlled via the descent button on the control box.
- Manual unilateral unlocking: Operated by the safety handle on the main post.
- Manual bilateral unlocking: Requires pulling a steel cable on the sliding table of the main or auxiliary lifting frame when lowering the lift.
1. Single Cylinder Hydraulic Two Post Car Lift
This type of lift typically has a lifting capacity of 3 to 4 tons and features a bottom plate design. Manual descent and unilateral manual unlocking are common, although electric unlocking and descent options are available (Figure 3). When the “up” button is pressed, the motor drives a gear pump to deliver high-pressure oil to the cylinder, which extends the piston rod. The chain, attached to a pulley at the top of the cylinder, lifts the main frame, which in turn raises the vehicle via arms mounted on the frame.
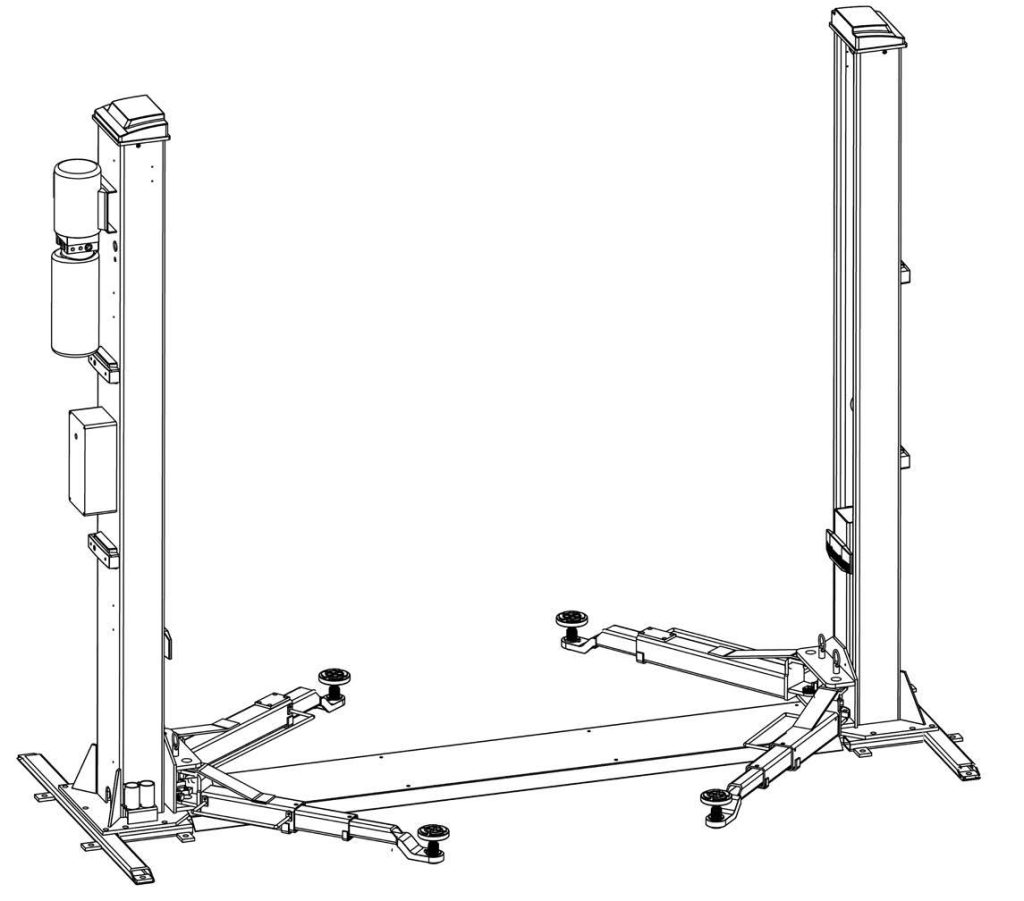
To lower the vehicle, the “down” button opens the lowering valve, allowing the hydraulic oil to flow back into the tank under the weight of the vehicle and the frame, controlled by a speed-regulating valve (Figure 4). The single-cylinder system includes various safety devices such as a mechanical locking system, chain break protection, and hydraulic overload valves. However, due to the challenges of maintaining synchronous lifting between the two frames, this model has been largely replaced by dual-cylinder hydraulic lifts.
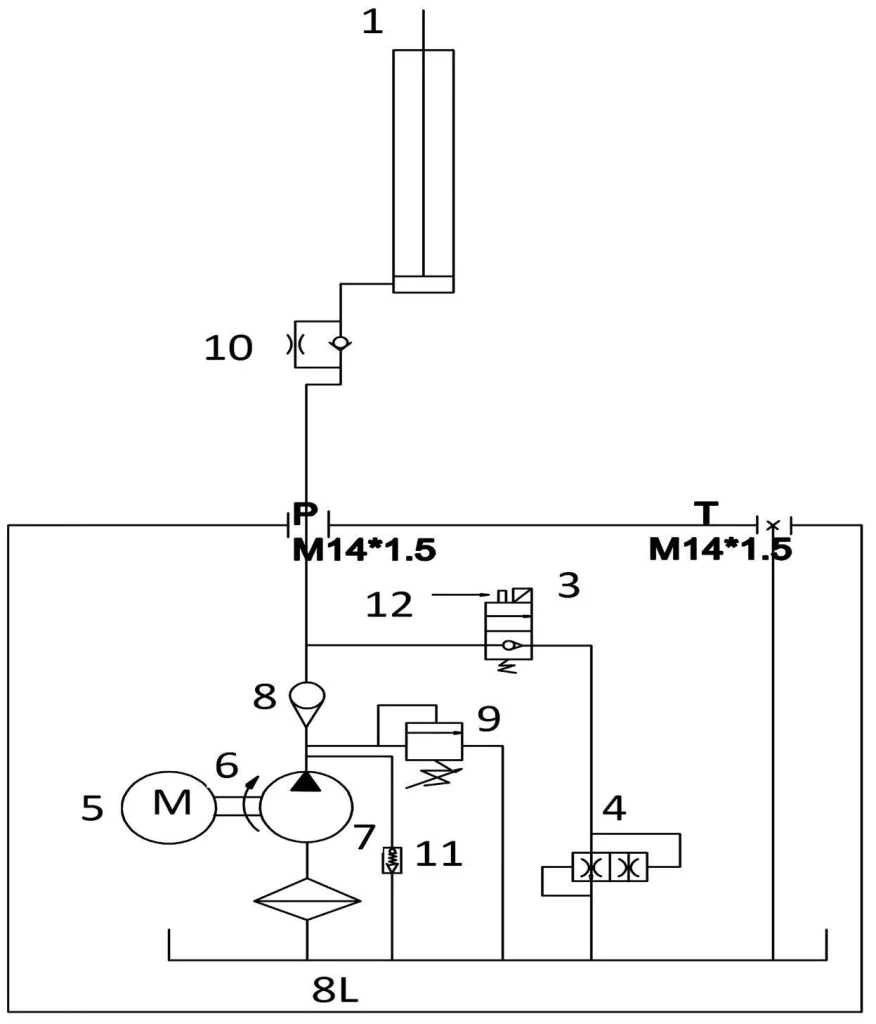
2. Dual-Cylinder Hydraulic Two Post Car Lift
Dual-cylinder lifts come in two main types: the gantry style(Figure 5) and the bottom plate style(Figure 6), with lifting capacities ranging from 3.2 to 8 tons. The gantry style, particularly for capacities over 5 tons, uses hydraulic cylinders in various configurations:
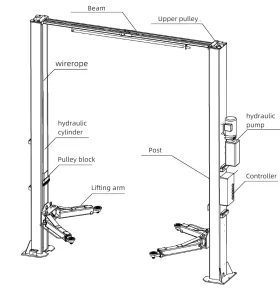
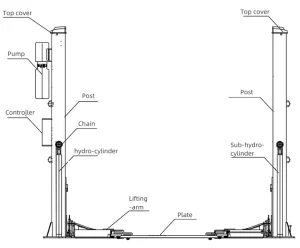
- Chain-driven double-cylinder: The cylinder stroke is half the lifting stroke.
- Direct-drive positive piston: The cylinder is located at the base, and the piston rod drives the upper support plate.
- Reverse-drive piston: The cylinder is inverted, and the lifting frame is driven by the movement of the cylinder.
The descent mechanism can be operated electrically or manually, with safety unlocking options available as electric, unilateral manual, or bilateral manual.
Most dual-cylinder systems use two equal-sized cylinders and balance steel cables to synchronize the lifting process (Figures 7 and 8).
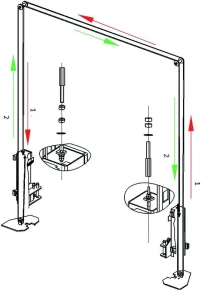
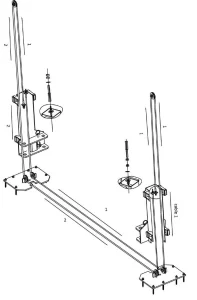
Key Maintenance Tips for Hydraulic Two Post Car Lift
1. Selection of Hydraulic Oil
Hydraulic oil is critical for the operation of these lifts. HM46 anti-wear hydraulic oil is suitable for temperatures between -9°C and 40°C, while HM32 oil is recommended for colder northern regions, where temperatures range from -15°C to 40°C. Oil should be replaced every 3 to 6 months initially, then annually or every 3,000 lift cycles. Neglecting timely oil replacement can lead to hydraulic failures, such as cylinder leaks or slow descent speeds, which may damage the system and shorten its lifespan.
2. Mechanical Lock
The mechanical lock, often located behind the lift’s post or within the sliding table, must be in good working order. Always ensure the safety lock is engaged before performing repairs beneath the vehicle. Failure to do so can result in serious safety risks, especially if the hydraulic cylinder malfunctions. Long-term reliance solely on the hydraulic system can also reduce the life of the cylinder.
3. Chains and Wire Ropes
As the primary load-bearing component, chains should be regularly inspected for wear. Foreign manufacturers recommend replacing chains every 3 to 4 years, and it is advisable to follow similar guidelines. Steel wire ropes, which ensure the synchronous operation of the lift frames, must also be checked regularly. If excessive wear or broken strands are detected, immediate replacement is necessary.
4. Routine Maintenance
Before each day’s work, inspect all safety mechanisms, such as the safety hook, locking teeth, steel wire ropes, and lifting pads. Regular checks of hydraulic cylinders, steel cables, and all moving parts should be performed every six months. If wear is observed on the slider (more than 1.5mm), it should be replaced. Anchor bolts must be tightened monthly, and chains and cables lubricated regularly.
Hydraulic oil should be replaced annually, and any issues with seals, oil leakage, or electrical components should be addressed by qualified technicians.